Cutting with diamond wire ...
A comparison of laboratory - saws that work with varying diamond wires:
Open end wire – saws
For a long time known they are the epitome of precision cuts for the sample preparation in microscopy. Extremely fine wires can be used (eg 100 microns in diameter) which makes it possible to cut very thin slices (the effective slice thickness depends on the material properties and can not be quantified). This saws work with low wire speed (eg, 2m/s), the contact pressure between wire and sample (gravity feed) is in the gram range (eg, 100g). No appreciable heat is created and in addition, the cutting wire is continuously wound on a metal cylinder, to whom he gives the residual heat. The cutting times are relatively long, which is, since the saw is designed for small samples, irrelevant. As the diamond wire constantly changes the cutting direction (the wire is typically 10m in length) a self-cleaning effect is created on the wire, but will also produce fine scratches (less than 5μm depth). The fluid is used solely for the removal of particles to keep the wire clean.
Endless wire saws
Still little known, since the introduction into the market just began, this saw type has unimagined applications. The wire speed is very high (typically 20 m/s), the cutting times correspondingly short. Hard materials such as glass and ceramics can be easily cut, the heat generated during cutting can be partially eliminated by a liquid (usually water). The wires range from 0.35 to 0.60 mm. Soft materials have a risk of sticking to the wire (by reducing the wire speed this can sometimes be prevented). If necessary, these saws can cut parts led by hand (shapes). It is of particular interest that in case of accidental touching the ongoing wire, no cuts on fingers are produced. This advantage is unique and not known from others saw types. The wire exchange can be accomplished very easily and quickly. Since the diamond wire runs in only one direction, the surface is largely groove – free. Normally this saw type is used in relation with electrical feed.
2010 we
The QUALITY vs. QUANTITY Issue
Qualityn
Well Diamond Wire Saws, Inc. believes quality is quantifiable
and our saws are designed, manufactured and perform to help others achieve
the quality results they seek. Regardless of the cutting task and
whether the application is for research and development, production, quality
control or failure analysis, Well Diamond Wire Saws, Inc. offers precision
cutting instruments that satisfy the most demanding cutting needs. We
invite you to explore our diamond wire cutting technology further.
The "Well" Design: Well Diamond Wire Saws
are designed to perform smooth cuts on virtually any material regardless
of its hardness, softness, brittleness, or pliability. The gentle cutting
action of the reciprocating diamond embedded wire ensures that the walls
of the cut material are both straight and smooth having negligible surface
roughness. For applications where the quality of the cut surface finish
is of significant importance, we believe there is no other cutting process
that offers this quantifiable result.
Cutting Methodology Wire Embedded with Diamonds
We use the highest quality stainless steel wire of various
diameters ranging from 0.055 to 0.60 millimeters. Then, through a proprietary
process, we embed diamonds of various grits sizes ranging from 10 to 64m
into the wire. The wire of between 10 and 40 meters length, depending
on the instrument, is then wound onto a precision-machined drum. The motor
that drives the drum saw reciprocates in its direction. For this reason
the part being cut must be mechanically clamped or "fixtured"
onto the stage or sample holder. Tensioning of the wire is achieved by
wrapping the loop of the diamond wire around a weighted pulley. As the
finite length, tensioned wire is wound onto the drum in both a forward
and reversed direction the diamonds gently remove material from the surface
in a straight, precise manner. The result is an extraordinarily smooth
surface with sharp corners.
Feeding the wire into through the sample
Since the minimum of force is applied to the sample,
either via gravity feed or via weights, the "Well" cutting procedure
insures consistent forces throughout the entire cut. It is acknowledged
that cutting times are somewhat longer than conventional cutting methods.
It must be determined whether the goal is to achieve a fast, often violent
cut or, as with the Well process whether a slower, gentler, and smooth
cut will produce the desired outcome. The slower cuts achieved with the
Well Diamond Wire Saws produce no measurable heat build-up commonly associated
with other cutting processes, therefore no coolant or cutting fluids are
required. Also, since virtually no "burning" of the sample occurs
during the cutting process both the odors and noise often accompanying
other methods is eliminated making the Well process environmentally acceptable
under the most stringent regulations.
Safety First
The diamond wire cutting tool travels at a relatively
slow rate of speed, which is continuously adjustable up to 2.5 meters
per second. This low rate of speed helps ensures a gentle cutting action
as well as makes the "blade" safe to the touch while the cut
is in process. In fact, the operator can watch the cut in process from
as closely as he or she desires since no protective hood is required.
Due to the low cutting forces employed the sample requires a bare minimum
of fixturing pressure. And, in the rare event of a wire breakage during
the cutting process, the machine immediately shuts off automatically.
Also, end-stop switches can be engaged to stop the saw either when the
cut is finished or when grooves of a defined depth are needed.
Quality2
In order to produce cutting instruments capable of delivering
precision, repeatable cuts Well Diamond Wire Saws, Inc. utilizes the very
best components available in every model saw it manufactures. Ever since
the company manufactured and delivered its first saw, the design and manufacturing
emphasis has always been to produce instruments that will operate 24 hours
a day, 365 days per year. Recently we learned that the first saw ever
delivered by the company is still in operation today. Regardless of whether
the instrument is made in our Mannheim, Germany or Le Locle, Switzerland
manufacturing facility, our personnel guarantee every instrument meets
and exceeds the highest quality standards.
United States:
Telephone: 770-582-9357
Fax: 770-582-9339
E-mail: wellsaws.dw@welldws.com
Address: Well Diamond Wire Saws,
Inc.
4708 S. Old Peachtree Road, 500 D
Norcross GA 30071 USA
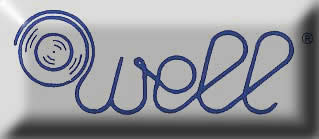
|